
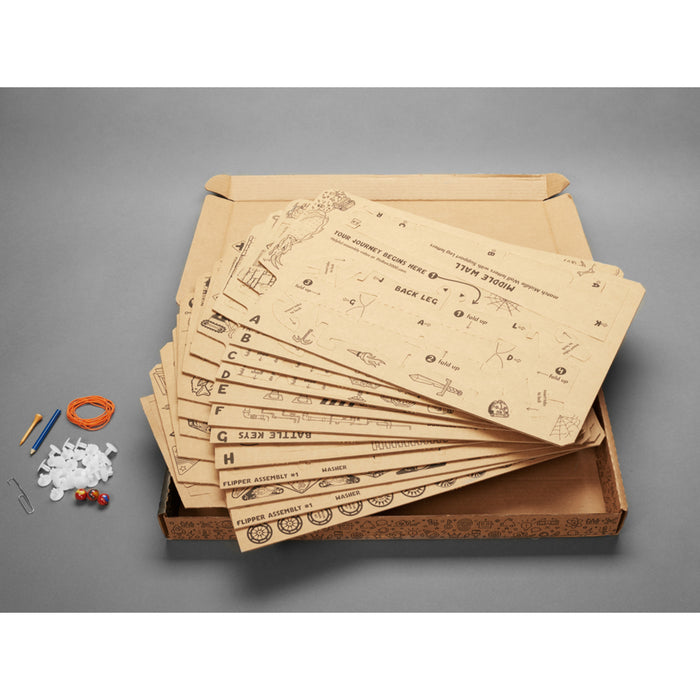
Plunger is a device for launching a ball. Also using 3D printer,it means additive fabriation. I designed many game objects in Rhinoceros, 3D Design tool. To create curved wall, I cutted MDF by laser cutter with repeated slit lines, so called kerf bending. Playfield, I mean the place ball will run around, are designed by mainly Adobe Illustrator, vector “2D Design”. This is one of my subtractive Fabrication. I made 2 parts but I used only underside for final project. Components and Fabrication ¶Ĭonsidering the size and production efficiency, I designed and made the enclosure during the week of Assignment8, Computer-Controlled Machining by using Shopbot. It contains not-analog, digital input sensors, buttons, flippers and pop bumpers. In my final project, I made wood-based small machine. Also some people tried to make in HTMAA/FabAcademy, but looks it couldn’t be completed. DIY makers made their own homebrew pinball machines, and there is some commercial homemade pinball kits. More detail and first initial plan are written in my tracking page and project development. Invention, intellectual property and income. This project and files for making is shared under Creative Commons CC-BY 4.0 license as I think Assignment18. You can play with this machine, launch styrofoam ball from 3D printed plunger, move flippers by pushing buttons, and if the ball passes certain points, photo reflectors detect it and pop bumper will bounce back the ball. My FAB-ALL PIN-BALL partially contains electronical mechanism and processing by microcontroller, input and output devices.
#PINBOX 3000 2 PLAYER PORTABLE#
So I decided to make small and portable pinball machine by digital fabrication techniques. I love pinball machines, But they are too big to put in my house. Invention, intellectual property and incomeĪlso you can see original files, slide and video.
